Una de las principales compañías productoras de papel en Brasil, con operaciones a gran escala y compromiso con la eficiencia operativa y la sostenibilidad. La empresa abastece a clientes nacionales e internacionales desde múltiples plantas, En línea con sus metas para 2030, buscaba una solución avanzada que le permitiera optimizar su consumo energético y garantizar la continuidad operativa, sin comprometer la calidad del producto.
Reducción del consumo de vapor, superando el objetivo inicial
Precisión del modelo predictivo del proceso productivo
Asertividad en la predicción anticipada de quiebra de papel
Precisión en detección de escenarios anómalos del proceso
Reducción de paradas no planificadas por cortes de papel
El desafío
La producción de papel enfrenta un equilibrio complejo: reducir costos energéticos sin sacrificar calidad ni estabilidad operativa. En la MP16, los principales desafíos incluían:
- Altos niveles de consumo de vapor, sin visibilidad clara de oportunidades de mejora.
- Falta de herramientas de predicción y ajuste dinámico, lo que resultaba en decisiones empíricas poco eficientes.
- Paradas no planificadas causadas por quiebres de papel, impactando la continuidad de la operación.
- Dificultad para integrar múltiples fuentes de datos (materia prima, clima, sensores) en una solución confiable y fácil de usar.
- La empresa requería una solución basada en inteligencia artificial capaz de anticipar comportamientos anómalos y optimizar el uso de recursos, manteniendo siempre la calidad del papel y minimizando el riesgo operativo.
¿Qué hizo Bruna?
Bruna implementó una solución integral de IA enfocada en dos objetivos clave: optimizar el consumo de vapor y anticipar riesgos operacionales como quiebres y anomalías de proceso.
Esto se logró mediante:
- Un modelo predictivo del comportamiento productivo con 98.21% de asertividad, capaz de recomendar ajustes por hora en 59 variables clave del proceso.
- Una red de predicción de quiebra de papel, que anticipa con 6 horas de anticipación eventos críticos con un 96.11% de precisión.
- Una red de detección de anomalías, con 99% de asertividad, que clasifica escenarios productivos normales vs. riesgosos y sugiere acciones correctivas inmediatas.
- Un sistema intuitivo para operadores, diseñado para facilitar la adopción operativa y asegurar una integración sin fricción.
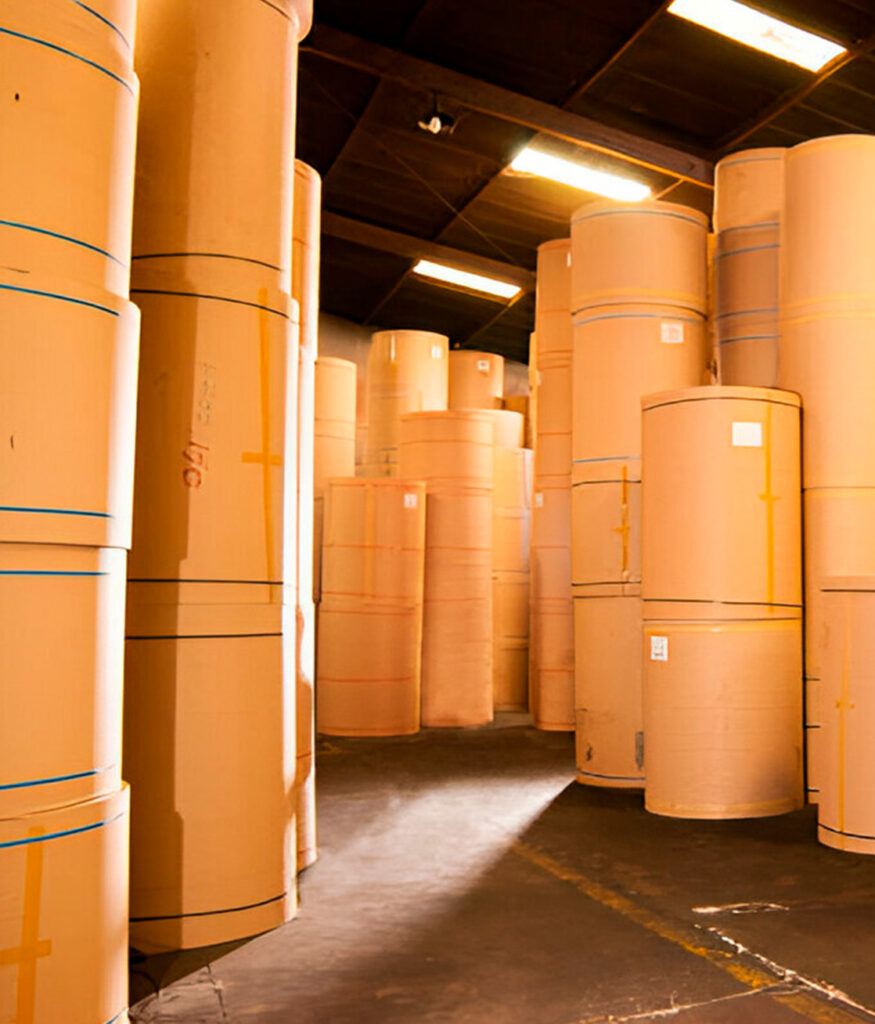
Los resultados
- 14.3% de reducción en el consumo de vapor, superando la meta inicial del proyecto.
- USD 420.000 ahorrados en consumo energético en solo tres meses de operación.
- 66% menos paradas no planificadas, gracias a la anticipación de eventos críticos.
- Mayor confianza del equipo de planta, al operar con predicciones claras y recomendaciones seguras.
- Predicciones de calidad y rendimiento en tiempo real, reemplazando decisiones empíricas con estrategias basadas en datos.