Esta empresa es una de las principales productoras de molibdeno en América Latina, con operaciones de procesamiento de concentrados provenientes de múltiples proveedores locales e internacionales. Su planta de oxidación representa una pieza clave en la cadena de valor, transformando materias primas en productos de alto valor para la industria metalúrgica y química global. Operando bajo estrictos estándares ambientales y de eficiencia, la compañía busca permanentemente innovar en el control de calidad, el uso de recursos y la estabilidad del proceso.
El desafío
Una operación minera dedicada al procesamiento de molibdeno enfrentaba importantes desafíos derivados de la alta variabilidad en la calidad de materias primas, que eran recibidas desde 28 proveedores distintos. Las demoras en los resultados de laboratorio —entre 4 horas y hasta 5 días— limitaban la capacidad de respuesta de los equipos operacionales, forzándolos a tomar decisiones reactivas basadas en promedios históricos.
Esta situación provocaba:
- Desviaciones de hasta 54% entre la calidad esperada y la real de la mezcla alimentada al reactor.
- Uso ineficiente del oxígeno, elevando los costos operativos.
- Ausencia de herramientas de simulación para evaluar escenarios o anticipar desvíos.
- Inestabilidad en la operación del reactor, afectando el rendimiento y la recuperación del molibdeno.
- Frente a estos desafíos, la compañía requería una solución tecnológica que entregara información confiable y oportuna para anticiparse a la variabilidad y optimizar el uso de recursos.
¿Qué hizo Bruna?
Bruna implementó su plataforma de predicción y optimización para abordar dos objetivos clave:
- Predicción de calidad de materias primas
Se desarrollaron modelos de inteligencia artificial para anticipar, con más de una semana de antelación, la calidad de los analitos críticos (Mo, Cu, Fe, W, Ca, Si y H2O). Esta solución eliminó la dependencia de promedios mensuales, entregando datos precisos y actualizados para cada lote de materia prima. - Optimización de mezcla al reactor
Se integró un módulo de optimización que sugiere en tiempo real las mejores combinaciones de materias primas, considerando calidad, stock disponible y restricciones operativas. Esto permitió alimentar el reactor con mezclas más homogéneas, mejorando el desempeño del proceso y reduciendo el uso de insumos críticos como el oxígeno.
Además, Bruna habilitó una herramienta de simulación de escenarios, que permite anticipar desvíos, planificar con mayor precisión y tomar decisiones proactivas.
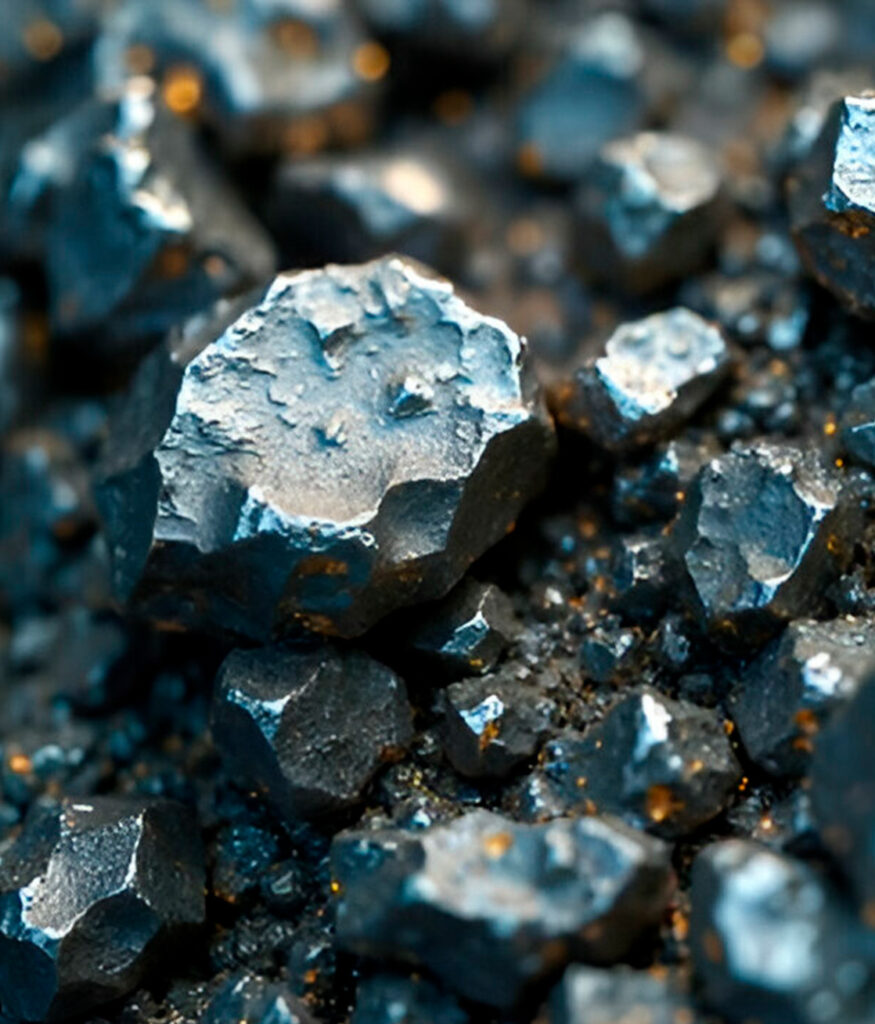
Impacto en la Operación
-
Precisión en la predicción:
Modelos con más de 97% de asertividad en la estimación de calidades de materias primas, permitiendo una planificación basada en datos reales. -
Reducción de consumo de oxígeno:
Gracias a las mezclas más homogéneas y precisas, el consumo de O₂ en el reactor disminuyó en 3.1%, generando un ahorro de USD 420,000 en tan solo 3 meses.
-
Reducción de consumo de oxígeno:
Se mejoró la utilización de materias primas, disminuyendo pérdidas y desviaciones. La herramienta de simulación redujo el tiempo de planificación y aumentó la capacidad de respuesta ante cambios de calidad.