Caso de negócios
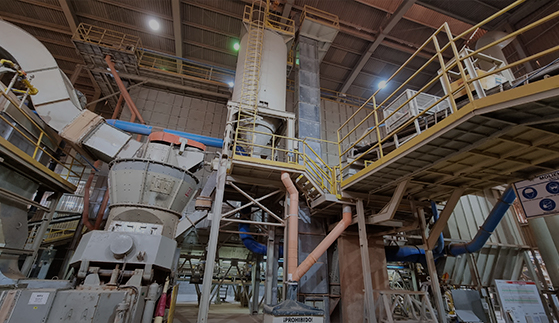

Cerâmica San Lorenzo (CSL)
Estudo de caso AI Bruna - Desenvolvido pela Altumlab
Cerâmica San Lorenzo (CSL) é uma das principais produtoras de revestimentos cerâmicos do Peru. Eles abastecem parte do mercado peruano, chileno e brasileiro. Em uma de suas fábricas há linhas de produção, onde é possível configurar a produção de um ou mais tamanhos de produto de acordo com a necessidade.
Para produzir cerâmica, uma mistura de argila e outros elementos é submetida a um tratamento de umidade que lhe confere propriedades coesivas, o que, juntamente com um procedimento em que ela é submetida a uma carga de alta pressão, forma o tamanho necessário.
As cerâmicas brutas, com sua cor avermelhada característica, são então encaminhadas ao longo de uma esteira transportadora, onde passarão por diferentes estações onde serão aplicadas bases de tinta, cores e acabamentos até chegarem à área de embalagem para serem armazenadas antes de serem despachadas.

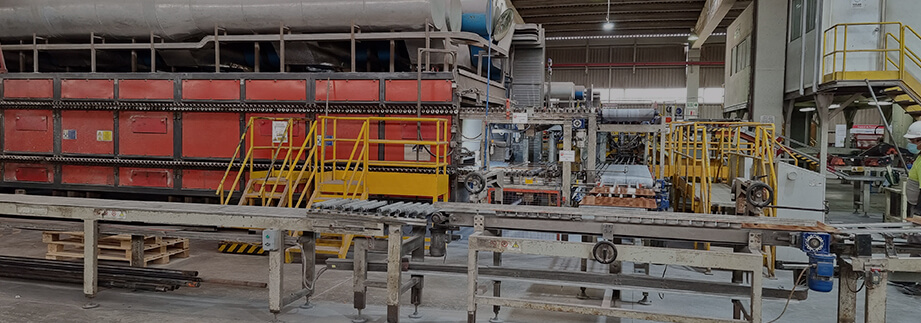
Os diferentes produtos são classificados por família de produtos, acabamento e seu respectivo tamanho ou formato. As linhas de produção devem ser configuradas cada vez que um produto é trocado de um para outro; no entanto, é possível reduzir o tempo de configuração quando dois produtos que compartilham o mesmo tamanho são produzidos consecutivamente, por exemplo, para usar esse tempo na produção.
A lógica de acoplamento de produtos "similares" deve considerar várias restrições comerciais e de produção, como volumes mínimos a serem produzidos cada vez que uma SKU é produzida, canal e satisfação do cliente, considerando que há prazos de entrega, prazos de remessa internacional e previsão de demanda por produto, por canal e por mercado.
Na fábrica, há uma equipe de planejamento que constrói e ajusta o que ou qual produto deve ser produzido em cada uma das linhas, tarefa exaustiva e altamente complexa, pois há mudanças diárias na demanda que impactam a produção previamente estabelecida.
Para resolver isso, o Chefe de Planejamento da CSL iniciou o desenvolvimento de uma estratégia que permitisse o uso de Inteligência Artificial para resolver esse problema. Como não havia nenhuma solução disponível no mercado, o centro de Pesquisa e Desenvolvimento AltumLab propôs uma possível solução, na qual, considerando a demanda comercial e as diferentes restrições operacionais, são projetados cenários de produção para cada linha.
No início, o projeto abrangeu uma fábrica, considerando linhas uniformes e multiformato. Isso deu início ao desenvolvimento de uma rede neural para otimizar o uso das linhas, considerando todas as restrições operacionais, dias e horas de operação, custos de produção por m2 por linha e a satisfação mínima por canal na previsão de demanda.
O planejamento de uma fábrica inteira pode ser executado constantemente sob demanda, onde os dados são consumidos diretamente de diferentes fontes e sistemas, como ERP, WMS, banco de dados e similares, economizando um tempo significativo no pedido e na coleta de informações.
Os resultados preliminares da solução permitem um aumento de 4% na produção com as mesmas instalações, mas com um sistema de planejamento dinâmico, em que, considerando cada venda realizada, é possível replanejar em questão de minutos o destino de cada linha, gerando valor adicional aos ativos disponíveis.